With the shortage of petroleum resources and the increasing environmental pollution, countries began to tighten their fuel consumption and emission standards. Therefore, more energy-efficient and environmentally-friendly vehicles began to be favored by people. For an internal combustion engine with a history of more than 100 years, if you want to continue to maintain its vitality, you must make a breakthrough in energy saving and emission reduction technology.
This article refers to the address: http://
From the perspective of technological innovations in the engine field by OEMs and component suppliers, miniaturized engines have long been the focus of chasing. Relatively speaking, smaller, more power-intensive engines can reduce friction losses and improve vehicle fuel economy. In addition, small-displacement engines of 1.6L and below in China can also enjoy preferential policies for halving the purchase tax.
What is the miniaturization of the engine?
Miniaturization of the engine reduces exhaust emissions and greenhouse gas emissions while improving fuel efficiency by reducing engine displacement or reducing the number of cylinders. Global emissions regulations and ever-increasing fuel economy standards are driving the development of traditional engines toward miniaturization. Currently, this technology is widely used in light gasoline engines by OEMs. Test data shows that engine miniaturization can increase fuel efficiency by 20% to 30%.
However, in the case of reducing fuel consumption and emissions, how does the miniaturized engine ensure that its power performance is not impaired during actual driving? The biggest question for the miniaturization of the engine is whether its power performance is strong enough, which also affects the miniaturized engine. The root cause of performance in the end market. Regarding the factors restricting the performance of the engine miniaturization market, Geshi Automobile will explain in depth in the later expert interviews, and this article will not go into too many details.
Engine miniaturization related technology
Smaller engines with fewer cylinders are possible, and are inseparable from key component technologies such as turbocharging technology, gasoline direct injection technology, and variable valve timing. The following is a brief analysis of the working principle of these technologies, and analyze the advantages and disadvantages of each technology.
Turbocharging technology
The turbocharger (Turbocharger) uses the exhaust gas emitted by the engine to impact the turbine to compress the intake air, thereby improving the engine's power and fuel efficiency.
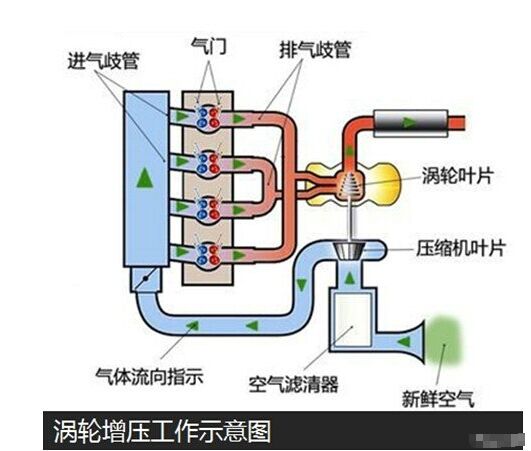
As we all know, the fuel needs to be ignited in the engine. The more oxygen, the more complete the combustion, the better the engine works. Turbocharging is a form of intake air for automobile engines. Its main function is to compress air and increase the intake air volume of the engine, thereby increasing the power and torque of the engine and making the car more powerful. At the same time, fuel combustion is more sufficient, fuel economy is improved and exhaust emissions are reduced.
When a turbocharger is installed in an engine, its maximum power can be increased by 40% or more compared to when the turbocharger is not installed. This means that the same engine can generate more power after being pressurized. Take our most common 1.8T turbocharged engine, after boosting, the power can reach the level of 2.4L naturally aspirated engine, but the fuel consumption is slightly higher than the 1.8L naturally aspirated engine.
Advantage:
1, have a good acceleration and sustainability, full of stamina. The maximum torque output has a wide range of speeds and a straight torque curve.
2. Improve fuel economy and reduce exhaust emissions.
3. Use the energy of the exhaust gas without consuming the power of the engine.
Disadvantages:
1. Ride comfort needs to be improved. At low speed, the turbine cannot be intervened in time, and there is a certain lag. Turbo hysteresis and non-linear power output are the biggest drawbacks of turbocharging.
2. The overall system temperature is increased and additional high heat effects need to be addressed. In order to solve the high heat impact, it is necessary to use a high temperature and oxidation resistant cooling and lubricating medium, and a cooler.
3. The maintenance cost is higher in the later period.
Therefore, when using a turbocharged engine, it is necessary to focus on the selection of engine oil and the oil change interval. The key bearings in the turbocharger need to be lubricated with engine oil and cooled with engine coolant. Most designs allow the engine coolant pump to continue working for a few minutes after a warm stop to cool the turbine cover. Since the turbine is driven by engine exhaust, the turbine cover may become red hot. In addition, since the oil has its established flow path, the oil is drained through these channels when the engine is turned off. Without proper cooling and emptying, the engine oil on the bearings burns (coking), turns into tar, and blocks the flow path of the oil, causing a catastrophic failure of the turbine.
Gasoline cylinder direct injection technology
Direct injection in the cylinder, as the name suggests, is the technology of directly injecting fuel into the cylinder and mixing with the air. Different from the traditional manifold injection, the direct injection in the cylinder further increases the injection pressure, making the fuel atomization more detailed, realizing the precise proportional control of the injection and mixing with the intake air, while eliminating the out-of-cylinder injection. Disadvantages. When the engine is low-speed and low-load, the injection is delayed, and the piston is injected at the final stage of the compression stroke. The air vortex is used to concentrate the fuel near the spark plug, and the stratified combustion achieves the purpose of fuel saving, but when the engine speed is up, the load is up. It is still necessary to inject in advance, and the fuel is injected into the intake stroke to uniformly mix and burn the oil and gas.
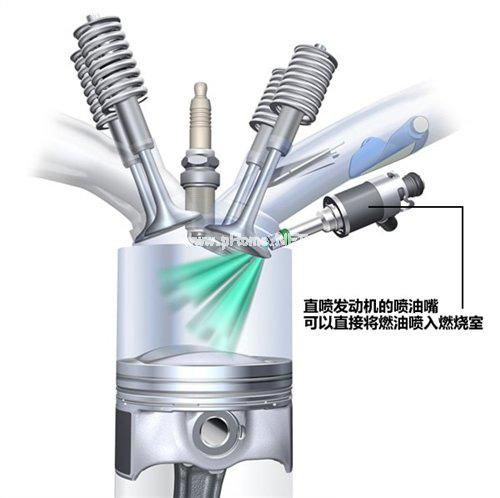
In addition, the special design of the nozzle position, spray shape, intake air flow control, and piston crown shape enables the oil and gas to be fully and uniformly mixed throughout the cylinder, so that the fuel is fully combusted and the energy conversion efficiency is higher. Compared to conventional PFI (port fuel injection) engines, GDI engine fuel consumption can be reduced by 20% to 50%.
Advantage:
1. Fuel combustion is more complete and energy conversion efficiency is higher.
2. More precise control of engine intake and injection timing to promote energy saving and environmental protection.
3. The transient response of the direct injection in the cylinder is fast and the startup is faster.
Disadvantages:
1. The combustion chamber is in an oxygen-rich environment and is prone to nitrogen oxides.
2, the combustion temperature is low, the three-way catalytic converter can not reach a good working temperature, the conversion of harmful media is not complete.
3. For the poor adaptability of oil, the sulfur in gasoline will poison the nitrogen oxide catalytic device.
Variable valve timing technology
The engine variable valve timing technology "VVT" (Variable Valve Timing), commonly known as "variable valve timing". The working principle is to adjust the amount of intake and exhaust according to the running condition of the engine, control the time and angle of valve opening and closing, so as to optimize the amount of air entering, thereby improving combustion efficiency.
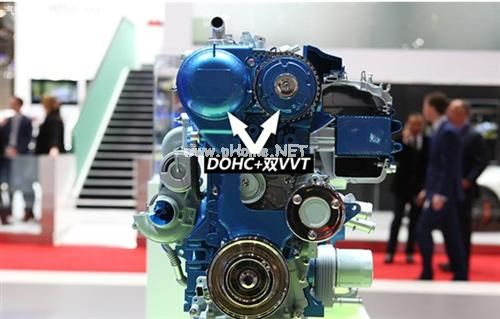
Generally speaking, the four-stroke gasoline engine is divided into four steps of inhaling, compressing, working, and exhausting. Because the engine is running at a high speed, a working stroke of a four-stroke engine takes only a few thousandths of a second. The time often causes the engine to have insufficient intake air and the exhaust gas is not clean, resulting in a drop in power. Therefore, it is necessary to utilize the intake inertia of the airflow, and the valve should be opened early and closed at night to meet the requirements of sufficient intake and clean exhaust.
A reaction turbine is a type of steam turbine that works on the principle that the rotor spins, as the name suggests, from a reaction force rather than an impact or impulse force.
In a reaction turbine there are no nozzles to direct the steam like in the impulse turbine.
Instead, the blades that project radially from the outer edge of the rotor are shaped and mounted so that the shape between the blades, created by the cross-section, create the shape of a nozzle. These blades are mounted on the revolving part of the rotor and are called the moving blades.
The fixed blades, which are the same shape as the moving blades, are mounted to the outer casing where the rotor revolves and are set to guide the steam into the moving blades. Below is a simple diagram of reaction turbine blades:
Reaction Turbine Principle:
In the case of reaction turbine, the moving blades of a turbine are shaped in such a way that the steam expands and drops in pressure as it passes through them. As a result of pressure decrease in the moving blade, a reaction force will be produced. This force will make the blades to rotate.
Reaction Turbine Working:
A reaction turbine has rows of fixed blades alternating with rows of moving blades. The steam expands first in the stationary or fixed blades where it gains some velocity as it drops in pressure. Then enters the moving blades where its direction of flow is changed thus producing an impulse force on the moving blades. In addition, however, the steam upon passing through the moving blades, again expands and further drops in pressure giving a reaction force to the blades.
This sequence is repeated as the steam passes through additional rows of fixed and moving blades.
Note that the steam pressure drops across both the fixed and the moving blades while the absolute velocity rises in the fixed blades and drops in the moving blades.
The distinguishing feature of the reaction turbine is the fact that the pressure does drop across the moving blades. In other words, there is a pressure difference between the inlet to the moving blades and the outlet from the moving blades.
Special Aspects of Reaction Turbines
- There is a difference in pressure across the moving blades. The steam will, therefore, tend to leak around the periphery of the blades instead of passing through them. Hence the blade clearances as to maintain as minimum as possible.
- Also, due to the pressure drop across the moving blades, an unbalanced thrust will be developed upon the rotor and some arrangement must be made to balance this.
Reaction Steam Turbine
Shandong Qingneng Power Co., Ltd. , https://www.steamturbine.be