Light-emitting diodes (LEDs) have the advantages of low energy consumption, power saving, long life and durability, so they are replaced by traditional lighting as future lighting sources. However, as the power increases, the waste heat of the electrothermal flow generated by the LED cannot be effectively dissipated, resulting in a serious decrease in luminous efficiency. LED service life is defined as the end of LED life when the LED luminous efficiency is lower than 70% of the original luminous efficiency. LED luminous efficiency will decrease with the use time and frequency, while too high junction temperature will accelerate the LED luminous efficiency attenuation, so the heat dissipation into LED is obvious.
   With the maturity of chip technology, the input power of a single LED chip can reach 5W or even higher, so it is more and more important to prevent the LED from operating too high. If the heat of the chip cannot be effectively dissipated, the thermal effect will become more and more obvious, which will increase the junction temperature of the chip, thereby directly reducing the photon energy emitted by the chip and reducing the light extraction efficiency. The increase in temperature also causes the spectrum emitted by the chip to red-shift and the color temperature quality to decrease.
   Assume that when the LED's pn junction temperature is 25 ° C (typical operating temperature), the brightness is 100, then the brightness is reduced to 80 when the temperature is raised to 75 ° C, and 60 to 125 ° C, to 175 ° C. Only 40 left. Obviously, the junction temperature is inversely proportional to the luminescence brightness.
   In addition to the quality of the lighting, high temperatures have a significant impact on LED life. The effect of temperature on brightness is linear, but the effect on life is exponential. Also based on the junction temperature, if it is kept below 50 °C, the LED has a service life of nearly 20,000 hours, and 75 °C only The remaining 10,000 hours of service life, 5,000 hours at 100 ° C, 2,000 hours at 125 ° C, 1,000 hours at 150 ° C. The temperature light is changed from 50 ° C to twice the 100 ° C, and the service life is shortened by 1/4 times from 20,000 hours to 5,000 hours, so the heat will greatly affect the service life of the LED.
LED heat dissipation has a great influence on luminous efficiency and service life. Therefore, the design of the heat sink is very important, and there are many problems that need to be overcome in derivative, and even become the key to the success of LED manufacturers.
   In-depth study of key points of LED heating
   Although the overall heat generation of the LED is not high, it is far more than other light sources when converted into heat per unit volume. The heat transfer path is mainly divided into three types, namely, conduction heat transfer, convection heat transfer, and radiation heat transfer. The dependence of LEDs on the three heat transfer methods is quite different. The LED can be dissipated from the air, and the thermal energy can be directly derived from the substrate or the thermal energy can be derived via the gold wire. If the eutectic and Flip chip processes are used, the thermal energy will be derived through the via hole to the system board.
   The proportion of heat flow in each part of the LED, the aluminum substrate (MCPCB) and the electrode lead (Lead) account for the largest proportion of heat flow. Since the temperature of the LED junction is much lower than that of other light sources, the thermal energy cannot be combined with the light in the radiation mode. Shot out, so about 90% of the excess heat of the LED is diffused outward by heat conduction. Under the action of high current intensity, the junction temperature of the LED chip rises, and a good LED package and module design are needed to provide proper heat conduction path for the LED. To reduce the junction temperature.
Source: However, although LEDs are highly dependent on conduction heat dissipation, LED packaging and other characteristics make conduction a major bottleneck in heat dissipation. How to overcome it is an important goal of many experts, such as "Thermal Analysis of Filp-Chip Packaged 280nm" The results of the simulation analysis of Nitride-Based Deep Ultraviolet Light-Emitting Diodes show that the bottleneck of heat dissipation is indeed the area of ​​the LED junction. The area of ​​the LED junction is too small, and the heat flux of the junction is quite large. The LED package is less prone to heat out quickly.
   Different packaging methods also have great influence. For example, some experts use SiC and Sapphire two different packaging methods, and use ANSYS's finite element software package to carry out thermal simulation analysis. The calorific value of the chips in two different packaging methods is 1W. In this experiment, the temperature distribution of the chip in the SiC package mode is relatively uniform, and the junction temperature is also low, which is related to the high heat transfer coefficient of SiC. Using the infrared thermal imager, the surface temperature of the chip in two different packages of SiC and Sapphire is actually taken. The maximum temperature difference of the chip surface of the SiC package is about 2 ° C, and the maximum temperature difference of the chip surface of the Sapphire package is about 43 ° C. In terms of thermal stress problems due to different thermal expansion coefficients, SiC packaging can achieve lower thermal stress.
   Thermal design typically has five control variations, LED spacing, dielectric thickness, circuit layer thickness, solder thickness, and ambient temperature. Usually the LED spacing is among the five control factors that affect the larger control factor. However, the LED pitch is not arbitrarily changed due to the optical design requirements of light mixing and light uniformity. In addition to the use of LED package and LED module design, the junction temperature is lowered, the LED life and reliability are increased, and the LED resistance to high junction temperature is also improved. However, in order to improve the heat dissipation of the LED after the process, it is still necessary. Consider the design of its thermal module.
   In addition, in addition to considering the chip temperature, LEDs still need to consider the thermal resistance (heat transfer to each transmission medium, the temperature difference generated on both sides of the medium, divided by the number of heating watts, the thermal resistance value can be obtained, heat The definition of resistance is similar to the resistance) to judge the heat dissipation efficiency. In the LED heat dissipation design, the overall package thermal resistance value of the LED needs to be reduced to ensure the stability of the component.
   Therefore, the high-brightness and high-power LEDs adopt the structure of the package to protect the junction position of the light-emitting part. The main heat-dissipation path for the heat dissipation of the LED junction is heat conduction. This point is started by the LED package design and materials, so that the junction temperature is easily transmitted. To the outside world. The LED module is designed to make the external heat easy to dissipate. Among them, the base part of the LED package is mostly made of a metal material, which has a high heat transfer coefficient and is a main route of heat conduction.
The LED package with good heat dissipation design and material matching needs to be matched with the well-cooled LED module design to effectively conduct heat to the external environment, and reduce the junction temperature to improve the luminous efficiency of the LED under long-term use. However, the basis of heat dissipation lies in the substrate.
   The high heat dissipation capability of the substrate is expected to grow rapidly despite the high cost.
   The main part of the LED's heat dissipation measures is that the LED die and the component itself carry the die of the die, and the LED component and the circuit substrate mounted on the system motherboard are strengthened. In practice, the LED is carried. The carrier plate of the die belongs to the key point that can be involved in the control of the LED package process, and the heat dissipation relationship between the LED component and the mounted circuit substrate is the focus of heat dissipation improvement of the general LED module factory.
   LED common substrates generally have four types: traditional and very mature PCBs, developing metal substrates (MCPCB), ceramic materials based on ceramic materials (Ceramic), and copper-clad ceramic substrates (DBC). The copper-clad ceramic substrate is a composite substrate formed by directly sintering a copper foil onto a ceramic surface. PCB and MCPCB can be used for general LED applications. However, when the unit heat flux density is high, the LED heat dissipation substrate mainly uses two types of metal substrates and ceramic substrates to enhance heat dissipation. The metal substrate is made of aluminum (Al) or copper (Cu) and can be classified into a "metal base" or a "metal core". The metal substrate process still needs one more insulation layer treatment. At present, the world's main thermal insulation rubber manufacturers are mainly American and Japanese.
   The other type is a ceramic substrate mainly composed of an insulating material such as AlN, SiC or BeO. Since the material itself is already insulated, it is not necessary to have an insulating layer. In addition, the ceramic substrate can withstand the breakdown voltage, the breakdown voltage (Break-down voltage) is also higher, in addition, its thermal expansion coefficient matching is good, can reduce thermal stress and thermal deformation is also an advantage, can be said to be quite suitable for LED applications At present, there are quite a few LED products used, but the price is still expensive, about 2 to 3 times that of metal substrates. Therefore, it is necessary to reduce the related costs.

Porcelain Station Post Insulator according to IEC, ANSI and other standards are used in substations and related switching equipment. Station Post Ceramic Insulator are produced in single piece up to 2300 mm and can operate voltages up to 1100KV in stacked configuration. High Voltage Station Post Insulator are subjected to compression, cantilever and torsional loads during service. Station Post Insulator for high voltagr use semiconductor glazes, so you don't have to worry about salt deposits or corona discharges.
Product Description
1.Material: Porcelain
2.Improved contamination performance
3.Widely applied to the line of different voltage classes
4.With features of good insulation performance
5.Long lasting durability
MAIN DIMENSIONS AND STANDARD PARTICULARS | |
Type | C4-125 |
Creepage distance(mm) | 430 |
Dry arcing distance(mm) | 200 |
Cantilever strength(KN) | 4 |
Tension Strength(KN) | 38 |
Torsion strength(N.m) | 800 |
Power frequency flashover wet voltage(KV) | 50 |
Impulse withstand voltage(KV) | 125 |
Net weight(KG) | 9 |
MAIN DIMENSIONS AND STANDARD PARTICULARS | |||
ANSI Class | TR-205 | TR-208 | TR-210 |
Creepage Distance/mm | 394 | 610 | 940 |
Cantilever Strength/kn | 8.9 | 8.9 | 8.9 |
Tensile Strength/kn | 38 | 44.5 | 53 |
Torsional Strength/k.m | 791 | 904 | 1130 |
Compression Strength/kn | 44.5 | 44.5 | 66.7 |
Low Frequency Dry Flashover Voltage/kv | 85 | 110 | 145 |
Low Frequency Wet Flashover Voltage/kv | 55 | 75 | 100 |
Critical Impulse Flashover Voltage, Pos/kv | 125 | 170 | 225 |
Critical Impulse Flashover Voltage, Neg/kv | 200 | 250 | 290 |
Low Frequency Dry Withstand Voltage/kv | 50 | 70 | 95 |
Low Frequency Wet Withstand Voltage/kv | 45 | 60 | 80 |
Impulse Withstand Voltage/kv | 110 | 150 | 200 |
Net Weight/kg | 7 | 11 | 16 |
Applicable Standard | ANSI C29.9 | ANSI C29.9 | ANSI C29.9 |
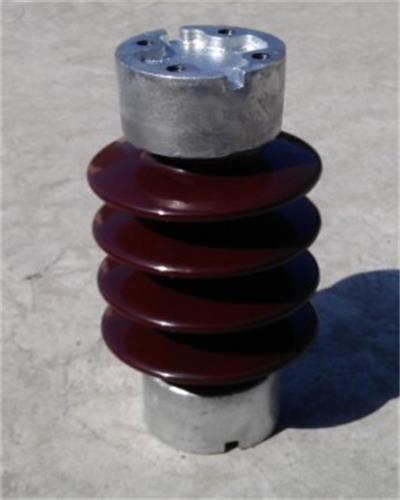

We warmly welcome friends both domestic and abroad to visit our company, if you have any questions, please contact with us directly.
Station Post Insulator
Station Post Insulator,Station Post Ceramic Insulator,High Voltage Station Post Insulator,Post Insulator For High Voltage
FUZHOU SINGREE IMP.& EXP.CO.,LTD. , http://www.cninsulators.com